Job costing is applied in the case of:
1. Job order costing is part of job costing normally applied to relatively small cost units e.g. repair of a motor vehicle in a workshop.
Steps taken to ascertain total cost and the price to charge
1. All the direct costs are charged to the job.
2. A share of overheads of each cost centre is charged by means of absorption rates.
3. When the job is complete it is put into the finished goods stores at factory cost.
4. When the job is delivered:-
a) A share of administrative and selling overheads are charged.
b) The difference between total costs and selling is the profit.
2. Batch costing it is a special type of costing whereby a cost unit consider of a group of identical items. In batch costing a job consists of units of similar products normally covered by a single number e.g. a catch of 5,000 text books. The procedure of batch costing is very similar to factory job costing or job order costing. It is a common method in engineering components industry, software clothing, printing etc.
3. Contract Costing This is part of job costing applied to those projects which are of a constructional in nature and where the period of completion is relatively long. The main examples include construction of building dams, bridges, roads etc. Contracts are normally large in size and extend over more than one accounting period. A significant part of the work is done at the customer?s site. A separate contract account is maintained for each individual contract. All costs incurred in order to complete a contract are charged to the specific contract.
Types of contract1. Fixed price contract it is where the contractor agrees with the contractee for a fixed contract price.
2. Cost plus contract In this case the contractor is reimbursed all the costs incurred plus a certain amount of money to cater for his profit. Such contractors are undertaken for the production of special products that are rarely manufactured.
3. Fixed price contract subject to escalation clause In this case the contractor is agrees with the contractor for a fixed contract price subject to escalation clause. This clause is provided to cover any changes in price of raw materials which can lead to a change in the price of the contract. However the contract is required to produce enough evidence of the excess cost incurred.
Methods of accounting for contractsThe principle problem relating to the accounting for constructional contracts is the allocation of revenue and the related cost to the duration of the contract. Normally two methods are used:
1. Completed contract method
2. Percentage of completion method
a) Completed Contract Method: In this case revenue is recognized when the contract is completed or it is substantially complete costs and progress payments are accumulated during the cause of the contract but revenues are not recognized until the contact activity is substantially complete. The risk of recognizing profit that may not have been earned is minimized under this method.
Definition of terms
1.
Direct expenses: They are incurred in addition to direct material and direct labour. They include hire charges of plant and machinery site office expenses site power etc. They are direct because they are easily identifiable with a particular contract.
2.
Direct materials: Materials charged to a specific contract may be classified as material issued from the store and materials purchased for a contract from the local market. Materials purchased and taken to the site direct together with those taken from the store are debited to the contract account. If some materials are returned to the store, the contracts account is credited. Material remaining on site re valued on cost and carried forward to the next period.
3.
Direct wages paid and accrued are debited in the contract account.
4.
Overheads: They include site telephone, electricity, repairs with etc. Overheads incurred on a specific contract are debited to the contract account or other overheads incurred for the company as a whole are apportioned on a suitable basis to all the contracts.
5.
Plants: This includes cranes, truckers, lorries etc., if plant is on lease basis leasing charges are directly charged to the contract account. If plant is purchased then purchase cost is charged to the contract for which it is purchased. At the end of the year or on the completion of the contact, the contract account is credited with the value of plant at that time. Depreciation is charged to the respective contract account. If plant is moved frequently from one contract to another then, each contract is charged with depreciation of the plant at a certain rate.
6.
Sub contract: Sometimes the contractor can assign some work to a subcontractor e.g. electrical work. The payment is charged to the debit of contract account.
7.
Architects certificates: Usually an architect inspects the work done periodically and certifies that the work is complete. He issues a certificate used by the contractor to claim payment. He is usually appointed by the contractee.
8.
Retention: A specific percentage of the work certified is usually withheld by the client and paid on completion. This is known as retention money. The purpose is to ensure that the work is completed by the contract to the satisfaction of the client and all defects are rectified. The amount retained is shown as debts in the books of the contractor.
4. Process Costing This is a form of operations costing used in cost where cost are passed through a series of processes before the product is finally completed. An inherent feature of process costing is that the output of one process becomes the input of the other process. In case of process costing all the cost direct and indirect are charged to the specific process. Process costing is normally used by industries which manufacture identical products such as chemicals, soap, spirits paper paint or products biscuits textiles etc.
Elements of process costing1. Raw materials
Material are divided into.
a) Input materials- materials introduced into the first process
b) Materials added- those added into subsequent processes
- The cost of all materials, input and added is debited in the process account.
2. Labour cost
- Labour cost of each process in debited in the process account. Labour cost is usually low in process costing due to automation
3. Direct cost
- These are expenses incurred in respect of my particular process.
4. Production overheads
- In case of production overheads each and every process is debited with a fair share of this production overhead.
5. Joint and By-Product Costing a)
Joint product costing these are products regarded to having substantially equal economic values and which arise from the semi process e.g.
i) In case of an oil refinery joint products include diesel, petrol, paraffin and lubricant.
ii) In the case of meat processing joint products include various grades of meat.
iii) In the case of daily products joint products include butter, cream and ghee.
Apportionment of joint cost - A problem arises as to how cost insured before separating the products is to be apportioned to the joint products. There are three methods adopted in this case:
i) Physical unit bases: In this case costs are apportioned according to the physical weight of the products. The method is suitable where products have an almost equal economic value.
ii) Sales value bases: In this case joint costs are apportioned according to the relevant sales value of the products. It is more suitable where items have different economic values e.g. in the case of silver, diamond.
iii) Net realizable: In this case joint costs are apportioned on the base of sales valueless post separation cost.
b)
By-Product Costing - A by product is a supplementary / secondary product which arises incidentally in the production of the main product and whose sales value is lower compared to the main product. In case of iron and steel manufacture the by-products are is furnace which is used in cement and brick manufacture. In case of meat trade by products are bones and grease. In case of timber trade by products are sawdust, small timber off cuts and barks. There are four ways of dealing with by-products in the books of account:
1. Net realizable value method
In this case the net realizable value of the by-product is detected from the total cost of the main product.
2. Receipts from the sale of the by-products are treated as incidental sources of income and taken to the general profit and loss account.
3. The sales of a by-product are added to the sales of the main product.
4. The by-product is treated as a joint product.
6. Service Costing This can be defined as a form of operations costing which appliers where standardized services are provided by an undertaking or a service cost centre within an undertaking. Service costing therefore is applied by organization which provides services rather than tangible goods examples include:
i) Road railway and air transportation.
ii) Power generation
iii) Hospitals- Local government services
iv) Hotel accommodation and Restaurant services may also be provided within an organization by department e.g. stores, maintenance, canteen etc.
- A principle problem in service cost is the determination of suitable cost unit to express cost. Each organization has a suitable cost unit for this purpose. Some common cost units used in respect of some services is as shown below:
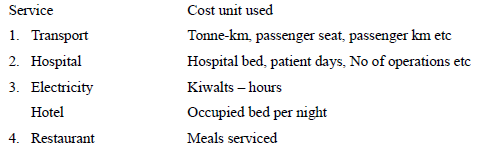
Wilfykil answered the question on
August 6, 2019 at 06:24