
Step 1. Establish performance standards. Standards are created when objectives are set during the planning process. A standard is any guideline established as the basis for measurement. It is a precise, explicit statement of expected results from a product, service, machine, individual, or organizational unit. It is usually expressed numerically and is set for quality, quantity, and time. Tolerance is permissible deviation from the standard. What is expected? How much deviation can be tolerated?
Step 2. Measure actual performance. Supervisors collect data to measure actual performance to determine variation from standard. Written data might include time cards, production tallies, inspection reports, and sales tickets. Personal observation, statistical reports, oral reports and written reports can be used to measure performance. Management by walking around, or observation of employees working, provides unfiltered information, extensive coverage, and the ability to read between the lines. While providing insight, this method might be misinterpreted by employees as mistrust. Oral reports allow for fast and extensive feedback.
Step 3. Compare measured performance against established standards. Comparing results with standards determines variation. Some variation can be expected in all activities and the range of variation – the acceptable variance – has to be established. Management by exception lets operations continue as long as they fall within the prescribed control limits. Deviations or differences that exceed this range would alert the supervisor to a problem.
Step 4. Take corrective action. The supervisor must find the cause of deviation from standard. Then, he or she takes action to remove or minimize the cause. If the source of variation in work performance is from a deficit in activity, then a supervisor can take immediate corrective action and get performance back on track. Also, the supervisors can opt to take basic corrective action, which would determine how and why performance has deviated and correct the source of the deviation. Immediate corrective action is more efficient;
however basic corrective action is the more effective.
An example of the control process is a thermostat:
Standard: The room thermostat is set at 20 degrees. Measurement: The temperature is measured. Corrective Action: If the room is too cold, the heat comes on. If the room is too hot, the heat goes off.
Titany answered the question on September 20, 2021 at 13:10
- Importance of Control in an organization(Solved)
Importance of Control in an organization
Date posted: September 20, 2021. Answers (1)
- Highlight six major purposes of controls in an organization(Solved)
Highlight six major purposes of controls in an organization
Date posted: September 20, 2021. Answers (1)
- Ways of facilitating communication(Solved)
Ways of facilitating communication
Date posted: September 20, 2021. Answers (1)
- Ways of improving organizational communication (Solved)
Ways of improving organizational communication
Date posted: September 20, 2021. Answers (1)
- Discuss three Forms of organizational communication(Solved)
Discuss three Forms of organizational communication
Date posted: September 20, 2021. Answers (1)
- Describe the Reinforcement theory of motivation(Solved)
Describe the Reinforcement theory of motivation
Date posted: September 20, 2021. Answers (1)
- Describe the David McClelland’s learned needs Theory of motivation(Solved)
Describe the David McClelland’s learned needs Theory of motivation
Date posted: September 20, 2021. Answers (1)
- Describe the Alderfer’s ERG Theory of motivation(Solved)
Describe the Aldermen's ERG Theory of motivation
Date posted: September 20, 2021. Answers (1)
- Limitations of the Hierarchy of Needs Model (Solved)
Limitations of the Hierarchy of Needs Model
Date posted: September 20, 2021. Answers (1)
- List three characteristics of learning organizations(Solved)
List three characteristics of learning organizations
Date posted: September 20, 2021. Answers (1)
- Describe three situational leadership theories(Solved)
Describe three situational leadership theories
Date posted: September 20, 2021. Answers (1)
- Forms of power used by managers to change employee behaviour (Solved)
Forms of power used by managers to change employee behaviour
Date posted: September 20, 2021. Answers (1)
- Identify the leadership styles found in the managerial grid model below
(Solved)
Identify the leadership styles found in the managerial grid model below
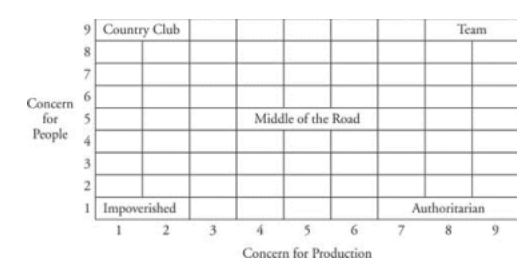
Date posted: September 20, 2021. Answers (1)
- Abilities that successful leaders possess according to Peter Drucker(Solved)
Abilities that successful leaders possess according to Peter Drucker
Date posted: September 20, 2021. Answers (1)
- Identify six core characteristics that the majority of effective leaders possess(Solved)
Identify six core characteristics that the majority of effective leaders possess
Date posted: September 20, 2021. Answers (1)
- Describe the importance of leadership in an organisation(Solved)
Describe the importance of leadership in an organisation
Date posted: September 20, 2021. Answers (1)
- Define directing in relation to leadership(Solved)
Define directing in relation to leadership
Date posted: September 20, 2021. Answers (1)
- Describe the employee compensation(Solved)
Describe the employee compensation
Date posted: September 20, 2021. Answers (1)
- Limitations of performance appraisal (Solved)
Limitations of performance appraisal
Date posted: September 20, 2021. Answers (1)
- List three components of performance appraisal(Solved)
List three components of performance appraisal
Date posted: September 20, 2021. Answers (1)