There are mainly two methods of costing
(1) Process costing
(2) Job order costing
1. Process Costing
Process costing systems are used for inventory costing where there is continuous mass production of homogeneous goods. Process costing systems use several work in progress (WIP) accounts, one for each process. This WIP accounts are referred to as process accounts and as goods move from one process to another their costs are transferred accordingly.
Process costing is less concerned with distinguishing among individual units of products but instead accumulates costs per period for each process (e.g. month)
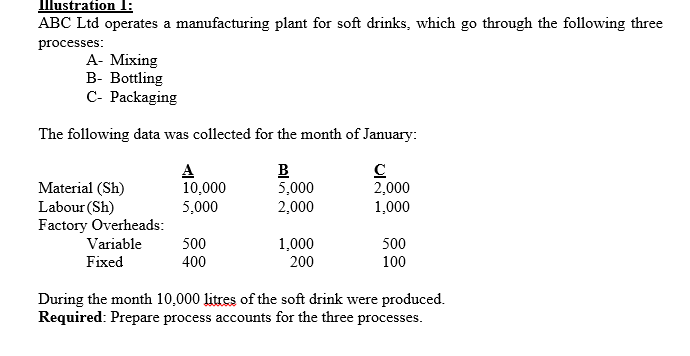
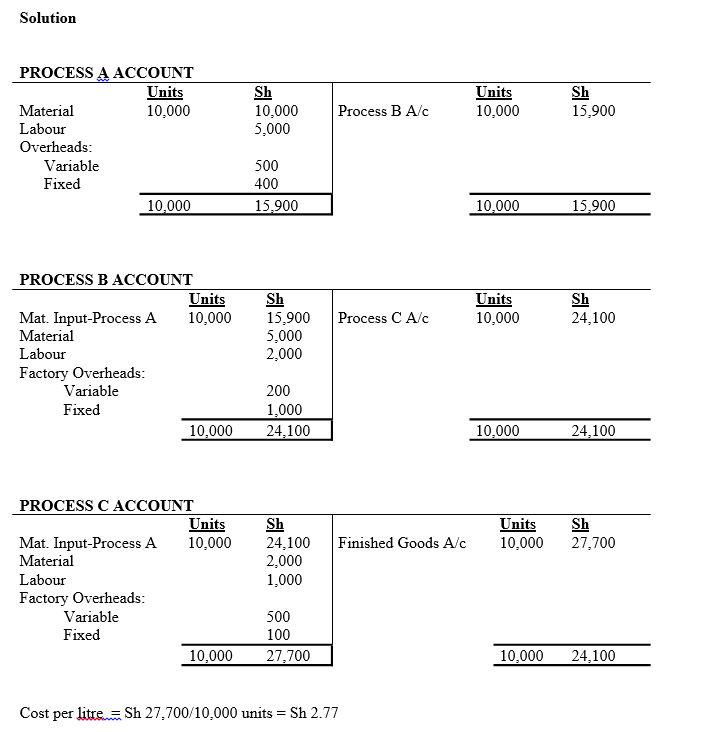
Steps in preparing a Production Cost Report
(i) Summarise the flow of physical units
(ii) Compute the output in terms of equivalent units (iii) Summarise the total cost per equivalent unit (iv) Compute the cost per equivalent
(v) Apply the total cost to the units completed and the units in the ending working in process
2. Job Order Costing
Job order costing is a method applied where a work is undertaken to customers’ special requirements and each order is of comparatively short duration. A job therefore is a cost unit that consists of a single order or a contract.
Procedures for Performance of Jobs
The normal procedures adopted in jobbing concerns involve the following:
(a) The prospective customer approaches the supplier and indicates the requirements of the job.
(b) A responsible official sees the customer and agrees with him the precise details (specifications) of the items to be supplied e.g. the quantity, quality, size, colour, date of delivery and any other special requirement.
(c) The organisation's department in charge of cost estimation prepares estimates for the job. This will include the cost of materials to be used, wages expected to be paid, the appropriate amount of factory, selling and administration overheads, the cost of additional equipment required if any and the organisation's profit margin.
(d) Loading the job on the factory floor to at the appropriate time. This occurs as soon as all materials, labour and equipment are available and subject to scheduling of other jobs.
Collection of Job Costs (Procedure)
1. Material requirements are send to stores
2. The material requisitions note (a source document) is used to cost the materials will be used to cost materials issued to the job.
3. The job ticket is passed to the staff members who are to perform the first operation; indicating the start time and completion time, and passed to the next staff until the last operation of the job.
4. Whether the job is completed or not the job ticket is send to the cost accounting office where the time spend will be recorded on the job cost card
5. The relevant cost of material used, direct labour costs and direct expenses are charged to the job account in the work in process ledger.
6. The job account is debited with the job share of the factory overhead based on the appropriate absorption rate.
7. On completion of the job the job account is charged with appropriate selling, administration and distribution overheads to ascertain the total cost of that job. The difference between the agreed selling price and the total cost incurred will be the producer's profit or loss.
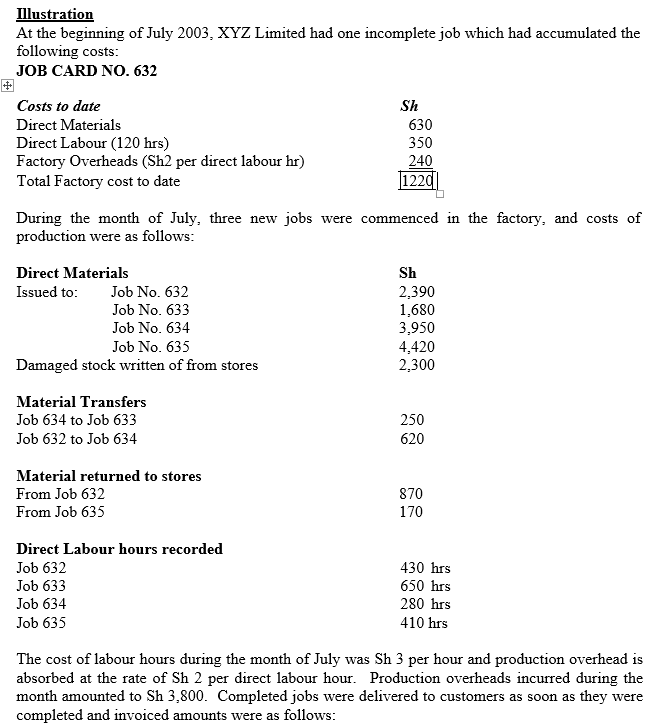
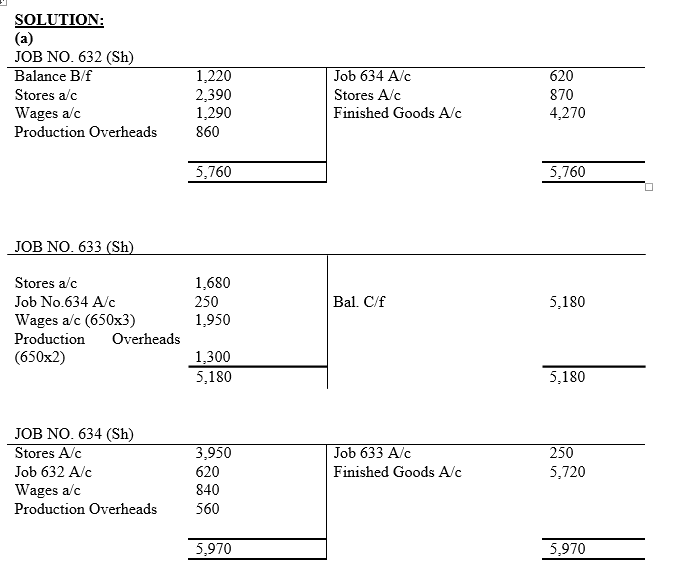
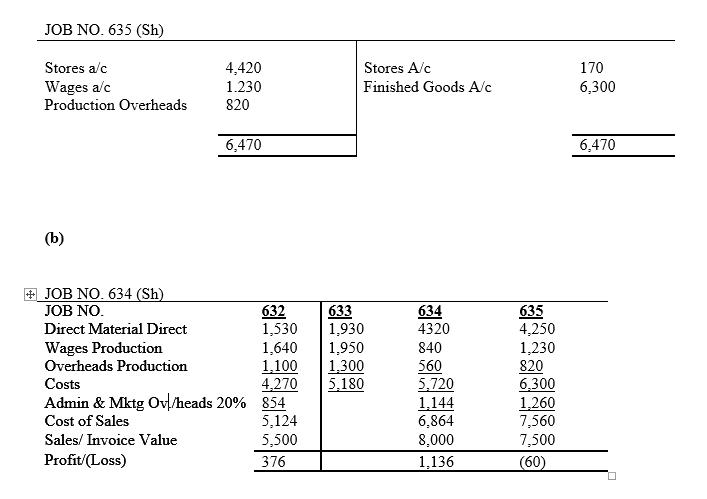
Titany answered the question on
October 12, 2021 at 12:05